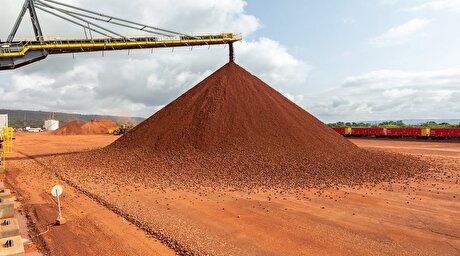
The new EWR system that will be installed along rolling mill #5 in Pingshan will start regular production in late Summer 2017.
It will weld, 12m long, 165mm square billets and ensure a mill productivity of 220 tph, for a continuous production of rebars from 10mm to 40mm.
The investment is expected to raise the rolling mill productivity by more than 10% and the material yield by 1.5%, at minimum.
Latest design features to be applied to the new welder includes the new extremely efficient Danieli spark killer system already in operation in a few plants in Europe and the United States.
The new device configuration is self-cleaning and very easy to maintain; it is able to collect more than 70% of spatter material generated during the flashing/welding cycle, dramatically reducing the amount of material spread along the welding run. It obviously results in a much “cleaner” welding unit, providing all the resulting benefits in terms of inspection accessibility and maintenance practice.
The L2 automation system – provided by Danieli Automation – ensures optimal control of all welding parameters, throughout the flashing and upsetting phases, in order to obtain perfect joints, well cleaned by a dedicated deburring station.
All in all, it is an effective and productive solution for establishing the ideal rolling conditions and producing top quality rebar material.
Once combined with Danieli K-Spool system, EWR-K welder allows the production hot rolled coils up to 5 tons.